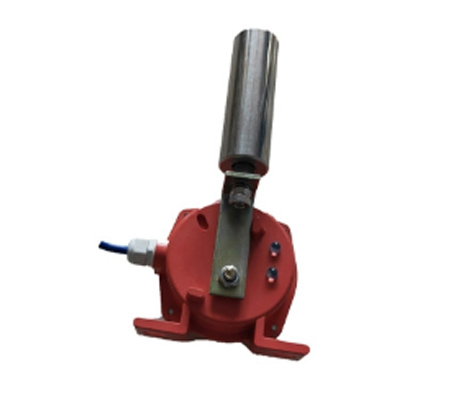
Product Overview
NST1-20-35 deviation switch is a high-performance industrial safety device designed specifically for conveyor belt systems, used for real-time monitoring and detection of conveyor belt deviation. This switch can quickly sound an alarm or automatically cut off power when the conveyor belt deviates, to prevent equipment damage and production accidents. NST1-20-35 adopts advanced sensing technology and durable materials, suitable for various industrial environments, especially for conveying systems in harsh working conditions.
Product Features
- High precision detectionThe NST1-20-35 deviation switch has high sensitivity detection function, which can accurately detect slight deviation of the conveyor belt and ensure the normal operation of the equipment.
- Durable materialsThe equipment casing is made of high-strength alloy or engineering plastic, which has excellent wear resistance and corrosion resistance, suitable for various industrial environments.
- High protection levelEquipped with IP65 protection level, it prevents the intrusion of dust and moisture, ensuring stable operation of the equipment in harsh environments.
- Easy to adjustThe detection angle and sensitivity can be adjusted according to actual needs to adapt to different conveyor belt systems.
- quick responseThe equipment can quickly respond when the conveyor belt deviates, issue an alarm or automatically cut off the power supply, effectively avoiding equipment failure and production interruption.
technical parameter
- model- NST1-20-35
- Detection angle: 15 ° to 30 ° (adjustable)
- contact rating: AC 220V 5A / DC 24V 5A
- Protection level: IP65
- working temperature-30 ℃ to+70 ℃
- Shell materialAluminum alloy/engineering plastic
- weight: 4.2kg
- Action torque: 20N·m
- response time:<1 second
working principle
The NST1-20-35 deviation switch is installed at key positions of the conveyor belt system, such as the head, tail, or turning points, to monitor the running status of the conveyor belt in real time. When a deviation of the conveyor belt is detected, the sensor will trigger a switch, issue an alarm signal or automatically cut off the power supply. This process can be completed in a very short time, ensuring quick response to abnormal deviation of the conveyor belt, avoiding equipment damage and production interruption.
application area
- miningA conveyor belt system used in industries such as coal mines and metal mines to monitor the status of the conveyor belt in real time and prevent equipment damage caused by deviation.
- Power industryApplied in the coal, fuel and other conveying systems of power plants to ensure the stable operation of the conveyor belt system.
- Chemical industryApplied in material transportation of chemical production lines to prevent safety issues caused by deviation.
- Metallurgical industryUsed for monitoring conveyor belts in metallurgical production such as steel and aluminum, providing reliable safety assurance.
Installation and Debugging
- Installation locationIt should be installed at key parts of the conveyor belt, such as the head, tail, and corners, to ensure comprehensive monitoring of the conveyor belt status.
- Angle and sensitivity adjustmentAdjust the detection angle and sensitivity of the equipment according to actual needs to adapt to different working conditions.
- Electrical wiringConnect the wires correctly according to the instructions to ensure the coordination between the equipment and the control system.
- functional testingAfter installation, perform a functional test to confirm that the equipment can accurately detect the offset of the conveyor belt and issue an alarm.
Maintenance and upkeep
- Regular inspectionRegularly check the working status of the equipment to ensure its normal operation.
- Cleaning equipmentIn high dust or humid environments, equipment should be regularly cleaned to maintain its sensitivity and stability.
- Lubrication and maintenanceProperly lubricate moving parts to reduce wear and improve service life.
matters needing attention
- Stable installationEnsure that the equipment is securely fixed during installation to avoid affecting its normal operation due to vibration or impact.
- Environmental adaptabilityThe equipment is suitable for various industrial environments, but prolonged exposure to extreme temperatures or highly corrosive environments should be avoided.
- Regular calibrationRegularly calibrate the equipment to ensure the accuracy of detection angle and sensitivity.
epilogue
The NST1-20-35 deviation switch has become an important tool for safety monitoring of conveyor belt systems due to its high precision, durability, and fast response capability. It can detect the deviation of the conveyor belt in real time and issue an alarm or cut off the power supply in a timely manner, effectively preventing production accidents and equipment damage. Whether in the mining, power, chemical, or metallurgical industries, NST1-20-35 can provide reliable safety guarantees for various conveyor belt systems.
Related Q&A FAQs:
1. What is the main function of NST1-20-35 deviation switch?
The NST1-20-35 deviation switch is used to monitor the deviation of the conveyor belt in real time. When the conveyor belt deviates from the normal track, the equipment will issue an alarm or automatically cut off the power to prevent equipment damage and production accidents.
2. How to adjust the detection angle of NST1-20-35 deviation switch?
The detection angle of NST1-20-35 can be adjusted within the range of 15 ° to 30 °. Users can adjust the settings on the equipment to match the desired detection angle based on the actual operation of the conveyor belt.
3. What are the requirements for equipment maintenance and upkeep?
This mainly includes regular inspections of the working status of equipment, maintaining equipment cleanliness, especially in high dust environments, and providing appropriate lubrication to moving parts to ensure long-term stable operation of the equipment.